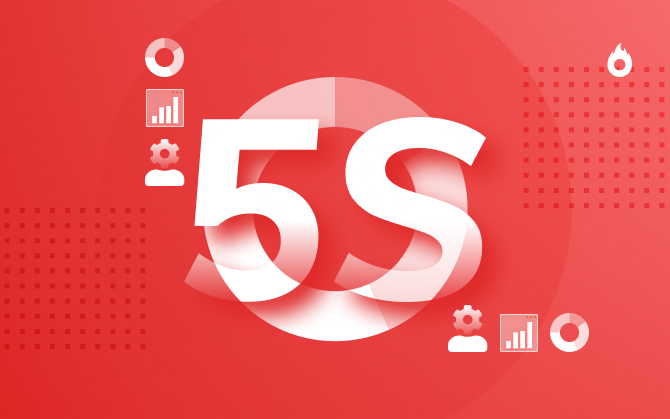
Learn all about the 5S methodology and how it can help you
Find out what this methodology can do for your business.
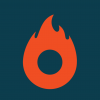
What will we see in this post
In the corporate world, there are several methodologies that focus on organization and increasing productivity.
Several studies aim to develop their own techniques so that factories, companies and even people can produce more and better.
One of these methodologies, known as the 5S methodology, has existed for a long time. However, it’s still one of the main management methods applied in major companies to this day.
Have you heard of the 5s? Do you know how it works and how it can help?
In this post, we’re going to tell you everything about it. Keep reading and check it out!
What is 5S methodology?
5s is often referred to as a technique, methodology, training or quality program. Regardless of the terminology chosen, the truth is that the 5s is a veritable management philosophy, which has the purpose of bringing about a profound change in the mentality of the employees involved in the work.
The concept originated in Japan, in a post-WW II context, in which Japan faced destruction after losing the war, along with the other countries of the Axis Power.
Thus, it was necessary to rebuild the nation, not only socially but also its production and economy.
The name 5S comes from the initials of five Japanese words used to explain and summarize the philosophy’s application.
Although they don’t have an exact translation in all languages, they have been translated into English as:
- Seiri — Sort;
- Seiton — Set in Order;
- Seiso — Shine;
- Seiketsu — Standardize;
- Shitsuke — Sustain/Self-discipline.
Developed by Sakichi Toyoda, founder of multinational Toyota, the 5S methodology sought to restructure Japan’s productive scenario by eliminating waste and the organization of companies in times of great shortages.
In this sense, several concepts and techniques were developed, such as the 5S. With its application, the concept of “just in time” production emerged, which helped the automaker expand its market on a global scale.
What are the characteristics of the 5S methodology?
The main idea behind the 5S methodology goes through the practices of continuous improvement, always seeking the improvement of processes and productive organization.
It helps in the creation and compliance with internal rules for each company and internal department, eliminating waste and developing healthy, safe and efficient work environments.
Although it sounds a little abstract, the 5S concept is actually easier to apply than you may think.
It consists of the full participation of all employees involved, who together analyze processes, objects and everything that is inserted in a certain space, assessing what can be eliminated in order to streamline production.
This analysis consists of the application of 5 distinct steps, which are treated as “senses”, in a free translation into English.
Seiri — Sense of Use
The first step of the 5S methodology application is the sense of use and disposal. It consists of sorting everything that is out of order in the working environment.
It’s a simple job of sorting and analyzing the current situation, assessing what already exists and identify what can be discarded and what must be kept.
Like all organization processes, the 5S requires this planning step, helping prepare for the arrival of changes.
Therefore, the Seiri step includes the analysis, identification of waste and the sorting of everything that isn’t useful.
Seiton — Sense of Organization
After performing the initial analysis, it’s time to get to work. The Seiton step contains everything remaining after the Seiri step, and that wasn’t identified as waste. From then on, all that is needed is a form of efficiently organizing these elements in the space available.
To do so, you can use ergonomic principles, making sure that each item is in its proper place.
The Seiton step should be applied to the company’s physical environment, from the president’s office to the “factory floor”, as well as to the virtual environment and documents. Everything must find its best place!
Seiso — Sense of Cleanliness
Analysis made, elements organized. The next step is keeping this environment clean and in order. And it’s within this context that the Seiso step comes in, the sense of cleanliness of the 5S methodology.
Tools, environments, machines, desks and other elements must be kept clean not only by employees or by the team directly responsible for the cleaning, but also by all those involved in the processes.
The sense of cleanliness requires, from all employees, the maintenance of one’s own workspace. In other words, ensuring a safe and healthy environment that minimizes the possibilities of problems occurring.
In addition to maintaining the space, Seiso also refers to the personal appearance of each employee. Everyone must be aligned with the company’s needs and the required standards.
Seiketsu — Sense of Standardization
As you can see, the first three steps of the 5S methodology correspond to a major cleaning of the productive environment, to put the house in order.
In this sense, the next step — Seiketsu —, consists of the transformation of the previous steps into something normal and routine.
Major companies may hire specific employees to handle the maintenance of these steps of the methodology, helping in the creation of a standard process.
In Seiketsu, all standards and values established in the previous steps must be fully absorbed by those involved.
Shitsuke — Sense of Discipline
The last S of the 5S has a deeper and more significant sense because it refers to each of those involved in this process of change and continuous improvement, developing in a very personal and individual level.
The idea behind the Shitsuke step is creating, in each employee, the sense of discipline capable of turning the entire 5S philosophy into a habit, practiced repeatedly.
This is one of the greatest challenges of the 5S methodology, because discipline is what makes the improvement of the productive environment truly continuous.
The most appropriate attitude for any business wanting to turn the 5S methodology into an internal work philosophy is to invest in the continuous training of their employees. That entails encouraging good practices and gradually, steadily establishing the methodology’s principles in everyday life.
Why you should apply the 5S methodology
Organization cannot be overlooked in any business. A lot of companies start using the 5S methodology in search for continuous improvement and as to ensure a safe, healthy and highly productive work environment.
More than applying ready-make techniques and recipes, the 5S philosophy aims to introduce the idea that an organized environment is capable of achieving major changes in any company.
This contributes to ensure resource savings, increase occupational safety and even positively influence employee motivation.
The 5S methodology is also directly responsible for increasing productivity and retaining customers, because it influences consumer satisfaction levels.
As if all of this wasn’t enough, in a context of increasing costs of physical spaces, the 5S philosophy also helps reduce the space necessary to produce at the same rate —, or even better.
In addition to the corporate work environment, the 5S methodology can be applied, with a few adaptations, to one’s personal life and career.
All one needs to understand is that each step corresponds to an important sense of change of thinking in one’s own life.
So, what did you think of the 5S methodology?
If you wish to learn more about management, you should also read our post with tips to develop your employees!